Linerless gurus, Ravenwood Packaging has unveiled its latest game-changing technology, the VXR, combining vision, x-ray and seal check technology. The new innovation will launch at Pro2Pac.
The new compact and high-tech arrangement provides an all-inclusive process for the seamless production of sleeving, contaminate detection and sealing of trays. Customers will benefit from fully automating their production lines, alleviating the need for manual checks which are costly in terms of manpower and time consuming when production deadlines are tight. These three technologies fall under the operation of just one machine, incorporated into just 1.9m. The ‘end of line’ solution provider to meet the food industry’s stringent requirements.
“Supermarkets are demanding improved quality, 100% error free labelling and reduced costs – placing increased pressure on suppliers,” says Paul Beamish, Founder and Managing Director of Ravenwood Packaging. “The new VXR machine will not only meet these demands but will outperform manual operations for a fully streamlined process.”
The key functionality of the VXR system, when combining the three technologies, is to identify and reject food trays that are seen to contain errors. Ravenwood’s VXR will solve these issues with ‘Sapphire’ carbon nanotube field emission technology. Sapphire is a leading technology in the field of x-ray, boasting low energy, high speeds and resolution for unparalleled performance.
Vision
With ‘Vision’, the machine automatically detects faulty labels, printing errors and poor quality print. Expect analysis of label position, quantity and orientation. All printed information is checked including barcodes, use-by dates and traceability codes. The system also boasts a user-friendly interface for rugged factory environments. Ravenwood stipulated this at the design phase. “The machine must be simple and easy to use,” said Beamish.
X-Ray
The VXR is programmed with heightened sensitivity for detecting dense mass and contaminates, and identifies foreign bodies such as glass, metal, ceramics including all types of bones. Products are cast aside and placed in the removable reject bin.
Seal Check
Contaminates in the seal are also screened, ensuring trays and food packages are properly sealed. Foods that have ‘slipped’ could potentially obstruct the seal. The system also examines for the correct position of the food and number of products within the tray – for example, number of meatballs.
“Contamination of food may pose serious consequences for a company. Under the Product Liability Law, every food producer is liable for contagions in the event that a consumer should be harmed,” adds Beamish.
Ravenwood is now taking orders. Machines are built bespoke to feature just one or all three of the technologies.
For further information, contact Natalie Bonner on +44 (0)1284 749144.
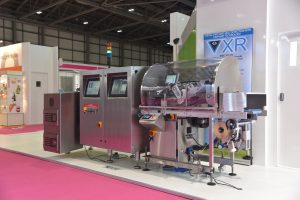
Ravenwood’s VXR machine ready for its grand unveiling at Pro2pac!
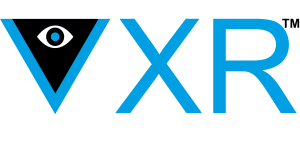
VXR logo