Ravenwood and its printer distributors have been producing shaped and die cut linerless labels for many years. And in recent months, we have been busy developing this concept further. We are now able to shape the leading edge of the label for a totally bespoke and creative look across all linerless label formats.
What is die cutting?
Die cutting has a long and interesting history and started out as an innovation in the 19th century as a way to cut patterns on materials such as paper, leather, rubber and fabric by hand. Fast forward to the 21st century and die cutting has certainly advanced, especially in the label industry. The technology has developed considerably and is now fully automated, infinitely more versatile and complex.
So how do you produce die cut linerless labels?
Our printer distributors can shape and punch out holes in both self-adhesive and linerless labels. The process for linerless is slightly altered in that shapes and areas that have been cut need extracting whereas with a standard label, supported by a glassine, the machine would only cut the shape on the face material, leaving the liner intact. Some of our printers have invested in print presses such as the Edale F3. The press would then have been modified for linerless to assist in the removal of pieces based on the agreed template or design. Modern die-cutting machines can now slice through a single layer on a label to the desired shape. Label materials include paper, card and film up to 300gsm.
How has Ravenwood advanced this technology?
During recent months, we have engineered this technology further and are now able to shape and modify the leading edge of the label fully as opposed to just punching out shapes on the face. Strict measures have been taken to ensure that all stages of the linerless process are uninterrupted and run smoothly throughout.
We have also adopted this new technology to our slideable sleeves. Our groundbreaking ‘slideable ready meal sleeve’ is a reinvention of the traditional cardboard sleeve yet comes supplied on a roll. In days gone by, the only way of applying a shaped or die cut sleeve was by hand but now thanks to Ravenwoods’ Nobac 500R applicator, the intensive application of hand-sleeving can now be made redundant. With automated sleeving, customers can benefit from reduced costs and labour.
So what are the benefits of die cutting and shaping linerless labels?
- Aesthetically pleasing
- More attractive presentation at POS
- Ingredients and food produce is presented in a creative way
- One of a kind design
Many high profile food manufacturers and brands like to feature shaped linerless labels on their products. A die cut label can provide a visually striking edge for making products stand out against the competition on busy supermarket shelves.
If you are interested in shaped and die cut linerless labels or would like some samples sent out to you, then contact us on +44 (0)1284 749144.
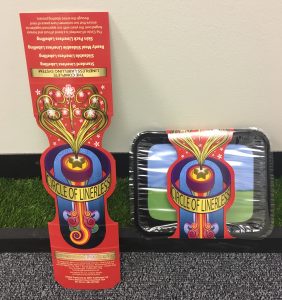
Die cut linerless labels. Request some samples today.
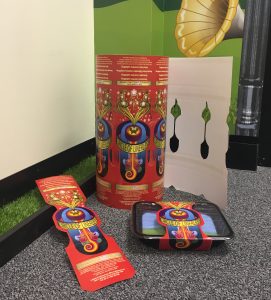
Die cut slideable sleeve
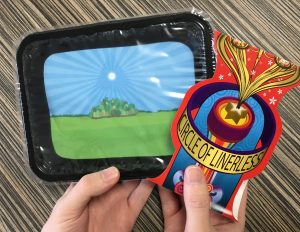
Our slideable sleeves come supplied on a roll!